FMEA steht für "Failure Mode and Effects Analysis" (Fehlermöglichkeits- und -einflussanalyse) und wird oftmals als FMEA Analyse bezeichnet, was der Übersetzung entsprechend eigentlich eine Dopplung beinhaltet. Es handelt sich dabei um eine systematische Methode zur Identifizierung, Bewertung und Reduzierung potenzieller Fehler oder Ausfallursachen in einem Produkt, Prozess oder System, bevor sie tatsächlich auftreten.
Die Risikoanalyse mit FMEA ist demnach ein proaktiver Ansatz, um die Qualität und Zuverlässigkeit von Produkten und Prozessen zu verbessern und potenzielle Risiken zu minimieren, bevor sie zu echten Problemen werden. Es ist wichtig, das Sie bzw. die verantwortlichen Mitarbeiter die FMEA-Tabelle regelmäßig aktualisieren und bei Bedarf weitere Analysen durchführen, um eine angemessene Risikobewertung und -verwaltung sicherzustellen.
Definition FMEA Analyse
Wie eingangs beschrieben, ist die FMEA Analyse bzw. Fehlermöglichkeits- und -einflussanalyse eine systematische Methode, um potenzielle Fehler oder Fehlerursachen in einem Produkt, Prozess oder System zu identifizieren, zu bewerten und zu minimieren.
Die FMEA-Analyse wird in verschiedenen Branchen und Bereichen eingesetzt, darunter Ingenieurwesen, Produktion, Qualitätssicherung und Projektmanagement. Das Hauptziel dieser Analyse besteht darin, potenzielle Probleme frühzeitig zu erkennen, um geeignete Maßnahmen zu ergreifen, um diese Probleme zu verhindern oder ihre Auswirkungen zu minimieren. Dadurch soll sich die Qualität, Zuverlässigkeit und Sicherheit eines Produkts oder Prozesses verbessert.
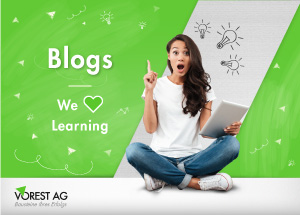
Weitere passende Blogbeiträge:
Entdecken Sie auch unsere anderen Blogbeiträge zur Qualitätssicherung und erhalten Sie Expertenwissen unter anderem zu diesen Themen:
Schritte zu Durchführung der FMEA Analyse
Der Prozess der FMEA-Analyse kann in mehreren Schritten durchgeführt werden. Hierzu verwenden Sie zur besseren Übersicht und Dokumentation ein FMEA Formblatt.
- Identifikation der zu analysierenden Elemente: Dies können Bauteile, Prozessschritte, Produkteigenschaften oder andere relevante Komponenten des Systems sein.
- Ermittlung möglicher Fehlermodi: Für jedes identifizierte Element werden potenzielle Fehler oder Ausfallarten ermittelt, die auftreten könnten.
- Bewertung der Auswirkungen: Für jeden Fehlermodus bewerten Sie die Schwere seiner Auswirkungen auf das Gesamtsystem. Sie ermitteln, welche Konsequenzen der Fehler für das Produkt oder den Prozess haben könnte.
- Identifikation der Ursachen: Das FMEA Team analysiert und ermittelt die Gründe für das Auftreten jedes Fehlermodus.
- Ermittlung der aktuellen Kontrollen: Die vorhandenen Kontrollen oder Vorkehrungen, die dazu dienen, den Fehlermodus zu verhindern oder zu erkennen, ermittelt das Team.
- Bewertung der Kontrollen: Die Wirksamkeit der vorhandenen Kontrollen wird bewertet, um zu sehen, ob sie ausreichen, um den Fehlermodus zu verhindern oder abzufangen.
- Berechnung des Risikos: Anhand der Bewertungen für Auswirkungen und Kontrollen berechnen Sie das Risiko für jeden Fehlermodus.
- Festlegung von Verbesserungsmaßnahmen: Falls das Risiko als zu hoch eingestuft wird, werden geeignete Maßnahmen zur Risikominderung oder Fehlervermeidung festgelegt.
Was ist die RPZ?
RPZ steht im FMEA-Kontext für Risiko-Prioritäts-Zahl. Die RPZ ist eine Kennzahl, die in der FMEA verwendet wird, um das Risiko eines Fehlers oder einer potenziellen Fehlfunktion zu bewerten. Die Risikoprioritätszahl wird normalerweise berechnet, indem drei Faktoren multipliziert werden:
- Schwere (S): Die Schwere beurteilt, wie schwerwiegend die Auswirkungen eines Fehlers oder einer Fehlfunktion sein könnten, wenn sie eintreten.
- Wahrscheinlichkeit (W): Die Wahrscheinlichkeit gibt an, wie oft oder wie wahrscheinlich es ist, dass ein Fehler tatsächlich auftritt.
- Entdeckung (E): Die Entdeckung bewertet die Wahrscheinlichkeit, dass ein Fehler während der Überwachung, Prüfung oder Kontrolle nicht erkannt wird.
Die Formel zur Berechnung der RPZ lautet anschließend: RPZ = S x W x E
Potenzielle Risiken mit höheren RPZ-Werten in der FMEA können Sie nun als kritischer einstufen und eine höhere Dringlichkeit für die Implementierung von Korrekturmaßnahmen zuweisen. Ziel ist es, die Risiken zu minimieren und die Zuverlässigkeit und Sicherheit des betrachteten Produkts oder Prozesses zu maximieren.
Welche Vorteile bietet die Fehlermöglichkeits- und Einflussanalyse?
Die FMEA Analyse bietet eine Vielzahl von Vorteilen und ist daher in vielen Branchen und Bereichen weit verbreitet. Durch ihre strukturierte Herangehensweise ermöglicht sie es Unternehmen und Organisationen, mögliche Fehler oder Ausfallursachen in Produkten, Prozessen oder Systemen zu erkennen, noch bevor sie tatsächlich auftreten.
Einer der Hauptvorteile der FMEA Analyse besteht darin, dass sie eine Früherkennung von potenziellen Problemen ermöglicht. Indem das Team mögliche Fehlermodi identifiziert und deren Auswirkungen bewertet, können proaktive Maßnahmen ergriffen werden, um diese Probleme zu verhindern oder ihre Auswirkungen zu minimieren. Dadurch verbessert sich die Produktqualität erheblich, was zu einer höheren Kundenzufriedenheit führt und langfristig Kosten einspart, da teure Reparaturen oder Rückrufe vermieden werden können.
Ebenfalls trägt die Fehlermöglichkeits und Einflussanalyse dazu bei, die Effizienz der Ressourcennutzung zu steigern. Indem das Team die Aufmerksamkeit auf die kritischen Bereiche lenkt, können Zeit und Geld gezielt eingesetzt werden. Dies fördert auch die Transparenz im Entwicklungsprozess, da potenzielle Risiken und Probleme für alle Beteiligten sichtbar werden. Dies erleichtert auch die Zusammenarbeit und Entscheidungsfindung.
Besonders in sicherheitskritischen Branchen wie der Luftfahrt oder der Medizintechnik spielt die FMEA-Analyse eine entscheidende Rolle. Sie trägt dazu bei, potenzielle Gefahren frühzeitig zu erkennen und zu beseitigen, was die Sicherheit von Personen und Anlagen gewährleistet. Zudem ermöglicht sie eine kontinuierliche Verbesserung von Produkten und Prozessen. Sie findet in verschiedenen Phasen des Lebenszyklus des Produktes Anwendung und fördert so eine ständige Optimierung. Neben der Qualitätssicherung unterstützt die FMEA Analyse ebenfalls das Risikomanagement in Unternehmen und Organisationen.
Insgesamt bietet die FMEA Analyse zahlreiche Vorteile, darunter die Verbesserung der Produktqualität, die Steigerung der Kundenzufriedenheit, die Kostenreduktion, die effiziente Ressourcennutzung, die Sicherheitssteigerung und die Förderung der kontinuierlichen Verbesserung. Sie ist ein wertvolles Werkzeug, um die Zuverlässigkeit, Qualität und Sicherheit von Produkten und Prozessen zu erhöhen und potenzielle Risiken proaktiv zu kontrollieren.
Interessante Produkte für Sie
Kursformen
Zertifikat
Informationen
Welche Ziele hat die FMEA Analyse?
Als Hauptziele der Fehlermöglichkeits- und -einflussanalyse können die nachfolgenden Punkte genannt werden:
- Früherkennung von potenziellen Problemen: Das Hauptziel besteht darin, potenzielle Fehlermodi oder Ausfallursachen frühzeitig zu erkennen, noch bevor sie tatsächlich auftreten. Dadurch können proaktive Maßnahmen ergriffen werden, um diese Probleme zu verhindern oder ihre Auswirkungen zu minimieren.
- Bewertung der Auswirkungen: Die FMEA zielt darauf ab, die Auswirkungen jedes identifizierten Fehlermodus auf das Gesamtsystem zu bewerten. Sie ermitteln, welche Konsequenzen der Fehler für das Produkt oder den Prozess bzw. die Prozesse haben könnte, um die kritischen Bereiche zu identifizieren.
- Identifikation der Ursachen: Ein weiteres Ziel ist die Identifikation der jeweiligen Fehlerursache. Dadurch ist ein besseres Verständnis für die Gründe geschaffen, warum bestimmte Probleme entstehen können.
- Ermittlung der aktuellen Kontrollen: Die FMEA analysiert die bereits vorhandenen Kontrollen oder Präventivmaßnahmen, die dazu dienen, den Fehlermodus zu verhindern oder zu erkennen. Dadurch überprüfen Sie, wie gut das System gegen potenzielle Fehler geschützt ist.
- Bewertung der Kontrollen: Mittels FMEA bewertet der Verantwortliche die Wirksamkeit der vorhandenen Kontrollen, um festzustellen, ob sie ausreichen, um den Fehlermodus zu verhindern oder seine Auswirkungen zu minimieren. Dadurch können Sie Lücken oder Schwachstellen im Sicherheitssystem untersuchen und entdecken.
- Berechnung des Risikos: Die FMEA berechnet das Risiko für jeden Fehlermodus basierend auf den Bewertungen für Auswirkungen und Kontrollen. Dadurch werden die kritischen Fehler priorisiert und die Aufmerksamkeit auf die größten Risiken gelenkt.
- Festlegung von Verbesserungsmaßnahmen: Falls das Risiko als zu hoch eingestuft wird, werden geeignete Maßnahmen zur Risikominderung oder -eliminierung festgelegt. Die FMEA unterstützt die Entwicklung von Strategien, um das Risiko zu reduzieren und die Produkt- oder Prozessqualität zu verbessern.
Insgesamt dient die FMEA dazu, die Qualität, Zuverlässigkeit und Sicherheit von Produkten und Prozessen zu verbessern, potenzielle Risiken zu minimieren und frühzeitig auf mögliche Probleme zu reagieren. Sie ist ein wichtiger Bestandteil im Qualitätsmanagement und in der Risikoanalyse.
Welche FMEA Arten werden unterschieden?
Eine der häufigsten FMEA-Arten ist die Design-FMEA (D-FMEA) bzw. Konstruktions-FMEA. Hier liegt der Fokus auf der Analyse von potenziellen Designfehlern während der Entwicklungsphase eines Produkts. Ziel ist es, mögliche Schwachstellen im Design bzw. in der Konstruktion zu erkennen und zu beheben, um die Produktqualität und Zuverlässigkeit des Produktes zu gewährleisten. Die D-FMEA ist besonders wichtig, da sich Fehler in der Designphase oft aufwändig und kostspielig in späteren Phasen korrigieren lassen.
Die Prozess-FMEA (P-FMEA) konzentriert sich auf die Analyse und Bewertung der Fehlermöglichkeiten in Fertigungsprozessen oder Dienstleistungen. Hier werden potenzielle Fehlermodi identifiziert, die während der Produktion oder Durchführung eines Prozesses auftreten könnten, und Maßnahmen ergriffen, um diese Fehler zu verhindern oder zu minimieren. Die P-FMEA ist ein wichtiges Werkzeug, um die Produktionsqualität zu steigern und Ausschuss zu reduzieren.
Für komplexe Systeme oder Produkte wird oft die System-FMEA (S-FMEA) angewendet. Hier werden mögliche Fehlermodi und deren Auswirkungen auf das gesamte System analysiert. Ziel ist es, potenzielle Risiken für das Gesamtsystem frühzeitig zu erkennen und geeignete Gegenmaßnahmen zu entwickeln.
Weitere FMEA Arten ist die Software-FMEA, welche speziell auf die Analyse von Softwareprodukten und -prozessen ausgerichtet ist. Sie ist in der Softwareentwicklung von großer Bedeutung, da Softwarefehler erhebliche Auswirkungen haben können. Bei der Zuverlässigkeits-FMEA liegt der Schwerpunkt auf der Bewertung und Verbesserung der Zuverlässigkeit eines Produkts oder Systems, indem Sie potenzielle Ausfallursachen analysieren und minimieren. Schließlich gibt es auch die Prozessablauf-FMEA, die sich speziell auf den Ablauf und die Schritte eines Fertigungsprozesses konzentriert.
Jede FMEA-Art hat ihre spezifischen Ziele und Anwendungsbereiche, aber sie folgen im Wesentlichen den gleichen grundlegenden Prinzipien. Die Wahl der FMEA-Art hängt von der spezifischen Situation und dem gewünschten Ziel der Analyse ab. Oft ist es vorteilhaft, verschiedene FMEA-Arten zu kombinieren, um eine umfassende Analyse zu erreichen.
Alle unsere YouTube Videos finden Sie hier auf dem YouTube Kanal der VOREST AG!
Wer führt die FMEA im Betrieb durch?
Die FMEA führt in der Regel ein interdisziplinäres Team durch, das aus Fachexperten verschiedener Bereiche besteht. Die Teammitglieder sollten über das notwendige Fachwissen und die Erfahrung verfügen, um die spezifischen Aspekte des zu analysierenden Produkts, Prozesses oder Systems umfassend zu verstehen.
Ein typisches FMEA-Team setzt sich aus Ingenieuren, Qualitätsmanagern, Produktmanagern, Fertigungsexperten, Risikomanagern und Vertretern des Kundendienstes zusammen. Jedes Teammitglied bringt seine individuelle Expertise und Perspektive in die Analyse ein.
Die Ingenieure spielen eine entscheidende Rolle bei der Identifizierung und Bewertung technischer Aspekte und möglicher Fehlermodi, die das Produkt oder den Prozess beeinflussen könnten. Die Qualitätsmanager bringen ihr Wissen über Qualitätsstandards, -prozesse und -methoden ein. Dies gewährleistet, dass die Analyse die Qualitätsanforderungen erfüllt und Fehler vermieden werden. Produktmanager liefern wichtige Informationen über Kundenanforderungen und -erwartungen, die das FMEA Team bei der Bewertung der Auswirkungen von Fehlern berücksichtigen muss. Fertigungsexperten haben Einblicke in den Produktionsprozess und können potenzielle Fehlermodi im Fertigungsbereich identifizieren.
Die Risikomanager bringen ihre Erfahrung im Umgang mit Risikoanalysen und -bewertungen ein. So stellen sie sicher, dass potenzielle Risiken angemessen bewertet und kontrolliert werden. Vertreter des Kundendienstes können dazu beitragen, mögliche Probleme im Zusammenhang mit Kundenerfahrungen und Rückmeldungen zu erkennen und zu berücksichtigen.
Die Durchführung einer FMEA erfordert eine sorgfältige und strukturierte Herangehensweise. Das Team sollte zusammenarbeiten, um alle relevanten Aspekte des zu analysierenden Elements zu berücksichtigen. Die Erfahrung und Expertise jedes Teammitglieds sind entscheidend, um eine umfassende und aussagekräftige Analyse zu gewährleisten. Die Zusammenarbeit eines interdisziplinären Teams ermöglicht es, verschiedene Blickwinkel einzubringen und eine ganzheitliche Bewertung potenzieller Risiken durchzuführen. Dies hilft, potenzielle Fehler oder Ausfallursachen frühzeitig zu erkennen und geeignete Maßnahmen zur Risikominderung oder -eliminierung zu ergreifen, um die Qualität, Zuverlässigkeit und Sicherheit des betrachteten Elements zu verbessern.
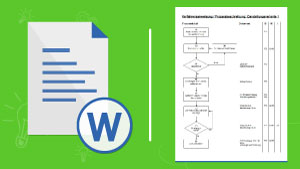
Kostenlose Vorlage -
Erstellung einer Prozessbeschreibung
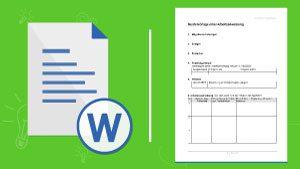
Kostenlose Vorlage -
Erstellung einer Arbeitsanweisung
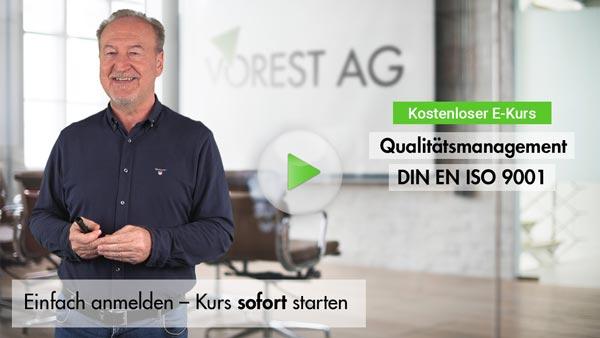
Kostenloser E-Kurs -
Was ist Qualitätsmanagement?
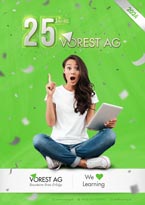
Unsere Serviceangebote im Bereich Qualitätssicherung
- Grundlagenwissen zum Thema: Was ist Qualitätssicherung? - Methoden, Definition und Aufgaben
- Ausbildungen & Weiterbildungen: Weiterbildung Qualitätssicherung & Methodenkompetenz Seminare
- E-Learning Kurse: Qualitätssicherung Online Ausbildung & QM Methoden E-Learning
- Inhouse-Training: Inhouse Schulung zu Qualitätssicherung & Methodenkompetenz bei Ihnen im Unternehmen
- Musterdokumente: Checkliste Qualitätssicherung und Methodenkompetenz Vorlage
- Wissensbausteine: Expertenwissen zu den QS Methoden, zur Qualitätssicherung und Methodenkompetenz
- Fachzeitschrift PRO SYS: Monatliche Fachinfos inklusive Musterdokumente
- Beratung: Wir unterstützen Sie beratend zu den QM Methoden und der Qualitätssicherung
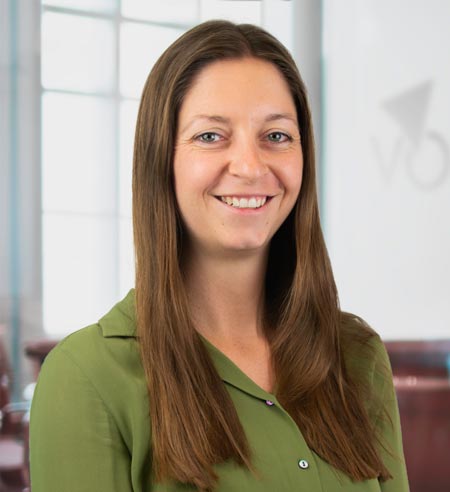
Ich helfe Ihnen gerne weiter!
Kati Schäfer
Produktmanagement Training & PRO SYS
Tel.: 07231 92 23 91 - 0
E-Mail: kschaefer@vorest-ag.de